Well, of a sort anyway... The story of my race car rebuild is being published in Practical Classics magazine, starting with the current issue.
Regular readers of these web pages will notice that the printed version has some catching up to do however which brings me neatly to the latest activity in and around my garage.
The other week a shiny piece of machined aluminium arrived. This was the special adapter I need to fit the clutch slave cylinder alongside my non-original gearbox (which I realise I still haven't written about here. I'll try to get around to it eventually!).
To fit this the engine and 'box had to come out again so I enlisted the help of my dad on an unseasonally dry day at the weekend. Getting the engine out was straightforward and fitting the new adapter went well too requiring only the removal of a small amount from the edge of the gearbox adapter plate and the filing off of a small lump on the bell housing casting.
Having reassembled the gearbox, adapter plates and bell housing, even the clutch release arm and pushrod didn't foul on anything which was most remarkable given the angle at which the pushrod now has to operate.
That angle is something of an issue though so the next stage will be to try and come up with a modification to the mechanism that allows the pushrod to be positioned more in line with the slave cylinder,
Here's a photograph taken from inside the bell housing and showing the angle that the pushrod is required to take up.
The angle becomes more acute as the release arm is pushed back towards its normal rest position.
The actual difference can be seen in this picture. The black line I've drawn indicates the alignment with the new slave cylinder.
I had a few ideas on how the pushrod pivot might be moved or redesigned but none of them make much sense so far. If anyone has any suggestions how this can be re-engineered, let me know.
Elsewhere I've been assured (again) that painting has started on my road car shell. That should now be back with me early next year, Hopefully...
Monday 26 November 2012
Friday 2 November 2012
Catching up
Just a brief update today to catch up on things.
I finished the modification to the floor of the car and then fabricated some seat mounting brackets from 3mm steel. There's almost no clearance at all around the brackets when the seat is installed but it all fits. Just.
Here's the promised photo of the finished floor repairs
Since I took that picture I've also welded in some strengthening plates for the seat mountings and painted it all red again.
The seat itself has gone back to Motordrive to be trimmed and finished.
Next job will be to refit the pedals and also to go back to working on the modified clutch arrangements to try and finish that job which was started many months ago. Unfortunately that means pulling the engine and gearbox out of the car again which probably means working outdoors. This is the wrong time of year to be trying to do that.
Away from the race car I finally got around to buying a new battery for the van last week so I got that fitted today. Once fitted it was good that the van started easily, given that I've not touched it for months. It was less pleasing when I discovered the alternator was completely seized with appropriate amounts of smoke pouring off the drive belts!
I'll pull the alternator when I get chance and see if it's fixable. Brief internet research suggests that they have a habit of rusting internally and can usually be cleaned up. It will be annoying if the bearings have dissolved as it's hardly been used since I fitted it as a replacement for the last alternator that destroyed its bearings.
I finished the modification to the floor of the car and then fabricated some seat mounting brackets from 3mm steel. There's almost no clearance at all around the brackets when the seat is installed but it all fits. Just.
Here's the promised photo of the finished floor repairs
Since I took that picture I've also welded in some strengthening plates for the seat mountings and painted it all red again.
The seat itself has gone back to Motordrive to be trimmed and finished.
Next job will be to refit the pedals and also to go back to working on the modified clutch arrangements to try and finish that job which was started many months ago. Unfortunately that means pulling the engine and gearbox out of the car again which probably means working outdoors. This is the wrong time of year to be trying to do that.
Away from the race car I finally got around to buying a new battery for the van last week so I got that fitted today. Once fitted it was good that the van started easily, given that I've not touched it for months. It was less pleasing when I discovered the alternator was completely seized with appropriate amounts of smoke pouring off the drive belts!
I'll pull the alternator when I get chance and see if it's fixable. Brief internet research suggests that they have a habit of rusting internally and can usually be cleaned up. It will be annoying if the bearings have dissolved as it's hardly been used since I fitted it as a replacement for the last alternator that destroyed its bearings.
Tuesday 16 October 2012
Creature Comforts
A couple of weeks ago I went to visit Motordrive Seats to try and sort out a race seat that would actually fit in the Spitfire. The Cobra seat I had before fitted pretty well but I thought I could improve on it.
Having spent a while talking to Allan at Motordrive about what could and couldn't be done I took away a bare seat shell for trial fitting. It's a very tight fit, as is everything on a car as small as the Spitfire, but it looks like it can be made to work.
The biggest issue was that to get the seat to go where I wanted it I've had to modify the floor of the car again. I'm quite tall and the floor is already lowered under the seat to allow me to get my head in under the roll cage for racing. To get the new seat in I needed to cut away the back of the lowered section and fabricate a new piece that extends the low part of the floor by a couple of inches.
All that sounds fairly simple. Just break out the grinder... The problem is that I hadn't been expecting to be doing serious metal surgery and the car is all fitted up with the new windscreen, dashboard, instruments and other things, not to mention the new paint. I've had to take great care not to embed grinding sparks in any of them.
Lack of space in the garage was also threatening to be a problem but a couple of consecutive weekends of good weather meant I could roll the car out of the garage and work in the sunshine which made a change!
Alternately attacking the floor with a cutting disc in the grinder and the Dremel for the awkward corners (plus judicious use of a large hammer) resulted in a hole in the floor of approximately the correct shape and size.
Another weekend's work saw the new metalwork fabricated and welded in place. I'll take a photograph next time I have chance to get the car outside (it's too dark in the garage). I'm quite pleased with the result although less so with the quality of my welding!
"Dry" fitting the seat seems to prove that it was worth all the effort so the next task will be to fabricate mounting brackets. As usual, none of the off-the-shelf ones will fit.
Just to add to the list of things to do, rolling the car back and forth has resulted in a nasty grinding noise at the back. I suspect one of my second hand Lobro joints in the rear axle is rather less healthy than I'd previously thought.
Having spent a while talking to Allan at Motordrive about what could and couldn't be done I took away a bare seat shell for trial fitting. It's a very tight fit, as is everything on a car as small as the Spitfire, but it looks like it can be made to work.
The biggest issue was that to get the seat to go where I wanted it I've had to modify the floor of the car again. I'm quite tall and the floor is already lowered under the seat to allow me to get my head in under the roll cage for racing. To get the new seat in I needed to cut away the back of the lowered section and fabricate a new piece that extends the low part of the floor by a couple of inches.
All that sounds fairly simple. Just break out the grinder... The problem is that I hadn't been expecting to be doing serious metal surgery and the car is all fitted up with the new windscreen, dashboard, instruments and other things, not to mention the new paint. I've had to take great care not to embed grinding sparks in any of them.
Lack of space in the garage was also threatening to be a problem but a couple of consecutive weekends of good weather meant I could roll the car out of the garage and work in the sunshine which made a change!
Alternately attacking the floor with a cutting disc in the grinder and the Dremel for the awkward corners (plus judicious use of a large hammer) resulted in a hole in the floor of approximately the correct shape and size.
Another weekend's work saw the new metalwork fabricated and welded in place. I'll take a photograph next time I have chance to get the car outside (it's too dark in the garage). I'm quite pleased with the result although less so with the quality of my welding!
"Dry" fitting the seat seems to prove that it was worth all the effort so the next task will be to fabricate mounting brackets. As usual, none of the off-the-shelf ones will fit.
Just to add to the list of things to do, rolling the car back and forth has resulted in a nasty grinding noise at the back. I suspect one of my second hand Lobro joints in the rear axle is rather less healthy than I'd previously thought.
Sunday 16 September 2012
A box of precision German engineering has arrived...
...and that's just the packaging!
These parts are the bits I need to complete the race car dashboard (well apart from the free pack of sweets at the top!). Most of them make up an instrument pod to house the gauges displaced from the centre of the dash by all my new switchgear.
A little work with glue and paint and it now looks something like this
Sorry for the not-too-great pictures. It's a bit dark in the garage.
I've also finished finished fitting the fire extinguisher control box at long last (that's it below the dash). I can now say that the fire extinguisher system is complete and so is the dashboard.
The next task will be to fit a seat. The one I have is really a bit too wide for the very narrow area between the sill and chassis rail on the Spitfire and I'd like to try and come up with something that will fit where I want it to go rather than fitting it in some way that it has to go because it's the only way it will fit. There aren't many race seats that will even come close to fitting in a Spitfire at all though. I've identified a couple of possibilities but need to do more research (and measurement) before spending a lot of money.
These parts are the bits I need to complete the race car dashboard (well apart from the free pack of sweets at the top!). Most of them make up an instrument pod to house the gauges displaced from the centre of the dash by all my new switchgear.
A little work with glue and paint and it now looks something like this
I've also finished finished fitting the fire extinguisher control box at long last (that's it below the dash). I can now say that the fire extinguisher system is complete and so is the dashboard.
The next task will be to fit a seat. The one I have is really a bit too wide for the very narrow area between the sill and chassis rail on the Spitfire and I'd like to try and come up with something that will fit where I want it to go rather than fitting it in some way that it has to go because it's the only way it will fit. There aren't many race seats that will even come close to fitting in a Spitfire at all though. I've identified a couple of possibilities but need to do more research (and measurement) before spending a lot of money.
Monday 3 September 2012
No, not that car, the other one
It's way past time I made an update here. Last time I wrote anything almost all progress on the race car had been stopped so I could pack up all the parts, store them and move all the parts of the road car out of storage to await the imminent arrival of the rolling shell.
Since then the rolling shell has completely failed to be finished, I still have a house full of parts and not much has happened except a lot of text messages and emails to try and establish what's actually happening with the shell (the answer to which seems to be "not very much" at the moment).
Not much to report then? Well I did manage to collect a lot of the remaining bits and pieces that had been left behind after the car was stripped and start refurbishing those.
For a start, here's the heater. The core seems to be intact or at least water passes through it from a hosepipe without leaking everywhere. I took that as a good sign. Flushing the matrix didn't produce masses of brown crud either so I removed thirty years accumulation of dead flies then cleaned it all up, tested the fan motor and painted the housing. Reassembly, as they say, is the reverse of the dismantling process
Next on the list was the fuel tank which proved to be remarkably free from internal rust and even had a tiny amount of petrol still in it after standing around for several years without the filler cap. I'm hoping that indicates a lack of leaks.
After getting rid of the remaining fuel there were a few flakes of (presumably) rust left behind so I flushed the tank with plenty of water from a hose and then dried it out. An old hairdryer I keep in the garage for these occasions fitted perfectly in the filler neck and, with the fuel level sender removed, provided a good flow of warm air through the tank to remove the moisture.
After that it was just a matter of cleaning up the outside of the tank and giving it a good coat of paint. The "before and after" pictures show a vast improvement.
I attended the TSSC International weekend at Stafford a couple of weeks ago. Apart from being a good weekend away I picked up a well worn looking fuel gauge for £2 and having got it home and cleaned it up it looks like a new part now so that's my entry for "bargain of the month" I think.
Progress on the race car hasn't been entirely zero. Whilst all this was going on I've obtained a CAD package and spent some time learning how to use it to produce a drawing of the adapter I need to be able to fit the clutch slave cylinder for the new gearbox. The next step is to try to turn the drawing into the actual item.
I've also started work on designing a new rear suspension upright. That's a longer term project in its own right and has thrown up a few challenges of its own, not least of which is my lack of skill at engineering drawing. I'll write more on this one once I have a better idea whether my plan has any chance of working.
Since then the rolling shell has completely failed to be finished, I still have a house full of parts and not much has happened except a lot of text messages and emails to try and establish what's actually happening with the shell (the answer to which seems to be "not very much" at the moment).
Not much to report then? Well I did manage to collect a lot of the remaining bits and pieces that had been left behind after the car was stripped and start refurbishing those.
For a start, here's the heater. The core seems to be intact or at least water passes through it from a hosepipe without leaking everywhere. I took that as a good sign. Flushing the matrix didn't produce masses of brown crud either so I removed thirty years accumulation of dead flies then cleaned it all up, tested the fan motor and painted the housing. Reassembly, as they say, is the reverse of the dismantling process
Smiths Heater - Exploded View |
After getting rid of the remaining fuel there were a few flakes of (presumably) rust left behind so I flushed the tank with plenty of water from a hose and then dried it out. An old hairdryer I keep in the garage for these occasions fitted perfectly in the filler neck and, with the fuel level sender removed, provided a good flow of warm air through the tank to remove the moisture.
After that it was just a matter of cleaning up the outside of the tank and giving it a good coat of paint. The "before and after" pictures show a vast improvement.
I attended the TSSC International weekend at Stafford a couple of weeks ago. Apart from being a good weekend away I picked up a well worn looking fuel gauge for £2 and having got it home and cleaned it up it looks like a new part now so that's my entry for "bargain of the month" I think.
Progress on the race car hasn't been entirely zero. Whilst all this was going on I've obtained a CAD package and spent some time learning how to use it to produce a drawing of the adapter I need to be able to fit the clutch slave cylinder for the new gearbox. The next step is to try to turn the drawing into the actual item.
I've also started work on designing a new rear suspension upright. That's a longer term project in its own right and has thrown up a few challenges of its own, not least of which is my lack of skill at engineering drawing. I'll write more on this one once I have a better idea whether my plan has any chance of working.
Thursday 19 April 2012
Odds and ends
Lots of odds and ends sorted out since my last update. Helped along by a long Easter weekend.
Having got the engine mounted properly I was able to finish making the mounting plate for the back of the gearbox. This is just a flat piece of 4mm steel drilled to mount onto the original chassis holes for the Triumph gearbox and then also drilled to accept the new gearbox mounting which is the same as a Ford type 9. A relatively easy job apart from having to dodge the rain showers whilst trying to apply paint.
I've also made up some proper mountings for the fuel tank. Previously it has always been mounted securely enough but I've never been entirely happy with the arrangement. A bit of fabrication with some aluminium box and angle has sorted that out.
Yes, there are a lot of blanking grommets in the boot floor! This car has seen a number of different tank mounting and plumbing arrangements over the years, plus all the holes that Triumph put there in the first place.
At some point I decided to fit two fuel pumps to the car. I don't entirely remember the reasoning behind this decision but it probably had something to do with protecting against pump failure during a race.
In any case, I fitted all the plumbing and finished the wiring for the pumps. The result now resembles a refinery but at least I shouldn't have a problem with fuel flow to the carbs!
There's just the last length of pipe to fit from the fuel filter out through the boot floor but I ran out of fuel hose at that point.
I've also finished building up the wiring harness for the engine bay and tested it. I'm happy to report that everything works except the horn and that's the fault of the horn itself (bought second hand "tested and working"!) rather than my wiring.
I think that the only electrical circuits I've not been able to test now are the radiator fan, water pump, water temperature sender and reversing lights. The first three because I don't have them on the car yet. The reversing lights because I broke a terminal off the switch whilst fitting it. A replacement is on order.
In between the bigger jobs I fitted a few external parts to the engine. When I came to fit the distributor I realised it still had a cheap "temporary fix" rotor arm in it. I have some good quality ones on the shelf so I fitted one of those but whilst doing that I noticed that the shaft didn't rotate smoothly.
That seemed odd, especially as the problem seemed to come and go at random as I spun the shaft. It seemed further investigation was in order. Stripping the distributor revealed that it was full of aluminium dust. It also revealed the reason why.
That screw, washer and spring washer were under the bottom plate that carries the advance weights and were gradually being thrown around and grinding away at the body. Part of the bottom plate was also bent.
I've no idea how long they've been in there. Obviously the engine has been running like that judging by the amount of swarf.
Once everything was cleaned and reassembled there was a screw missing from the baseplate at the top so presumably that's where the errant one came from.
Whilst reassembling I realised I'd failed to take note of which way round the drive dog was supposed to fit so I've no idea whether I've refitted it correctly or 180 degrees out. I'll have to check before fitting the unit to the engine.
The distributor cap also broke when I put that back so I'll have to try and track down a source of good quality replacements. The spare I have on the shelf is made of really thin and nasty plastic.
Next job is to borrow an extra pair of hands to complete the wrapping of the front sections of the wiring loom. After that there are a couple of light bulbs and a replacement horn to fit but I don't think there are many more big jobs to do before I stop work on this car in order to start on the other one.
That's not to say I won't have thought of a few more by next week mind you!
Having got the engine mounted properly I was able to finish making the mounting plate for the back of the gearbox. This is just a flat piece of 4mm steel drilled to mount onto the original chassis holes for the Triumph gearbox and then also drilled to accept the new gearbox mounting which is the same as a Ford type 9. A relatively easy job apart from having to dodge the rain showers whilst trying to apply paint.
I've also made up some proper mountings for the fuel tank. Previously it has always been mounted securely enough but I've never been entirely happy with the arrangement. A bit of fabrication with some aluminium box and angle has sorted that out.
Yes, there are a lot of blanking grommets in the boot floor! This car has seen a number of different tank mounting and plumbing arrangements over the years, plus all the holes that Triumph put there in the first place.
At some point I decided to fit two fuel pumps to the car. I don't entirely remember the reasoning behind this decision but it probably had something to do with protecting against pump failure during a race.
In any case, I fitted all the plumbing and finished the wiring for the pumps. The result now resembles a refinery but at least I shouldn't have a problem with fuel flow to the carbs!
There's just the last length of pipe to fit from the fuel filter out through the boot floor but I ran out of fuel hose at that point.
I've also finished building up the wiring harness for the engine bay and tested it. I'm happy to report that everything works except the horn and that's the fault of the horn itself (bought second hand "tested and working"!) rather than my wiring.
I think that the only electrical circuits I've not been able to test now are the radiator fan, water pump, water temperature sender and reversing lights. The first three because I don't have them on the car yet. The reversing lights because I broke a terminal off the switch whilst fitting it. A replacement is on order.
In between the bigger jobs I fitted a few external parts to the engine. When I came to fit the distributor I realised it still had a cheap "temporary fix" rotor arm in it. I have some good quality ones on the shelf so I fitted one of those but whilst doing that I noticed that the shaft didn't rotate smoothly.
That seemed odd, especially as the problem seemed to come and go at random as I spun the shaft. It seemed further investigation was in order. Stripping the distributor revealed that it was full of aluminium dust. It also revealed the reason why.
That screw, washer and spring washer were under the bottom plate that carries the advance weights and were gradually being thrown around and grinding away at the body. Part of the bottom plate was also bent.
I've no idea how long they've been in there. Obviously the engine has been running like that judging by the amount of swarf.
Once everything was cleaned and reassembled there was a screw missing from the baseplate at the top so presumably that's where the errant one came from.
Whilst reassembling I realised I'd failed to take note of which way round the drive dog was supposed to fit so I've no idea whether I've refitted it correctly or 180 degrees out. I'll have to check before fitting the unit to the engine.
The distributor cap also broke when I put that back so I'll have to try and track down a source of good quality replacements. The spare I have on the shelf is made of really thin and nasty plastic.
Next job is to borrow an extra pair of hands to complete the wrapping of the front sections of the wiring loom. After that there are a couple of light bulbs and a replacement horn to fit but I don't think there are many more big jobs to do before I stop work on this car in order to start on the other one.
That's not to say I won't have thought of a few more by next week mind you!
Monday 16 April 2012
Suspension Turret Comparison
Well the engine is finally in properly. It turned out that I had somehow acquired a Spitfire suspension turret on the right hand side of the car and a non-Spitfire one on the left.
Apparently all the "small chassis" Triumph cars apart from the Spitfire and the very early Herald 948 use the same suspension turrets. The Spitfire has a slightly different design which makes the front of the engine sit lower down to clear the low bonnet line. I'm told that the early Herald has a completely different design but I've not seen an example of those.
Thanks to all those I spoke to about the problem and those who posted in reply to my query on the Club Triumph web forum. Also thanks to Pete at Yorkshire Triumphs who let me loose in his yard with a tape measure to compare the parts fitted to various cars.
In the end it became obvious that (early Herald excepted) there are two different left hand turrets and two different right hand ones. To fit a Spitfire engine, you need a matched pair of Spitfire turrets. To perform the common conversion of fitting a six cylinder engine in a Spitfire chassis ideally you need a matched pair of non-Spitfire turrets. It does seem though that this conversion can be performed if you only change one side which probably means there are more cars out there with mismatched turrets.
There seems to be very little information published on what the differences in these parts actually are. (Either that or I've been looking in the wrong place!). Having got both parts together I took some photographs and measurements in the hope that they will be useful for anyone else with similar problems.
First of all, here's the two turrets side by side and viewed from the inside, that is the side that normally faces the engine. The Spitfire part is on the right of this picture.
The only difference appears to be the engine mounting on the front of the turret. You can see in the picture that the Spitfire engine mounting is visibly lower.
Of course that wouldn't be obvious if you don't happen to have both parts to hand to compare them. Fortunately there seems to be an easy way to tell which kind of turret you are looking at.
On the Spitfire turret, the engine mounting face is flat with a small raised flange at the end. The non-Spitfire one has a crease running vertically down the centre.
There are also differences in the dimensions. These pictures didn't turn out quite as well as I'd hoped but the Spitfire engine mounting is lower and also further inboard.
The measurements will vary between the left and right hand turrets as the engine mounting faces are different from one side to the other however both sides have the flat face mounting for the Spitfire and the mounting with the crease otherwise.
Hopefully this will help prevent someone else falling over the same issue I had. Once the correct part was fitted the engine bolted in easily.
Apparently all the "small chassis" Triumph cars apart from the Spitfire and the very early Herald 948 use the same suspension turrets. The Spitfire has a slightly different design which makes the front of the engine sit lower down to clear the low bonnet line. I'm told that the early Herald has a completely different design but I've not seen an example of those.
Thanks to all those I spoke to about the problem and those who posted in reply to my query on the Club Triumph web forum. Also thanks to Pete at Yorkshire Triumphs who let me loose in his yard with a tape measure to compare the parts fitted to various cars.
In the end it became obvious that (early Herald excepted) there are two different left hand turrets and two different right hand ones. To fit a Spitfire engine, you need a matched pair of Spitfire turrets. To perform the common conversion of fitting a six cylinder engine in a Spitfire chassis ideally you need a matched pair of non-Spitfire turrets. It does seem though that this conversion can be performed if you only change one side which probably means there are more cars out there with mismatched turrets.
There seems to be very little information published on what the differences in these parts actually are. (Either that or I've been looking in the wrong place!). Having got both parts together I took some photographs and measurements in the hope that they will be useful for anyone else with similar problems.
First of all, here's the two turrets side by side and viewed from the inside, that is the side that normally faces the engine. The Spitfire part is on the right of this picture.
The only difference appears to be the engine mounting on the front of the turret. You can see in the picture that the Spitfire engine mounting is visibly lower.
Of course that wouldn't be obvious if you don't happen to have both parts to hand to compare them. Fortunately there seems to be an easy way to tell which kind of turret you are looking at.
On the Spitfire turret, the engine mounting face is flat with a small raised flange at the end. The non-Spitfire one has a crease running vertically down the centre.
Non-Spitfire turret |
Spitfire turret |
Non-Spitfire. Shorter top flange |
Spitfire. Longer top flange |
Non-Spitfire. Taller from chassis to engine mount |
Spitfire. Much lower from chassis to engine mount |
Hopefully this will help prevent someone else falling over the same issue I had. Once the correct part was fitted the engine bolted in easily.
Sunday 25 March 2012
How do you know if an elephant's been in your fridge?
A weekend spent mostly lying upside down where the driver's seat should be with my head under the dashboard has resulted in all the wiring and plumbing under there being completed. It has also resulted in the somewhat unusual phenomenon of footprints on the roll cage!
Both fire extinguisher and battery are now fully fitted and I've tested all of the wiring that I can at this stage. The good news is that it all works! There were a few minor things wrong but they were soon sorted out. Specifically;
The headlight flash didn't work due to two terminals on the switch being the wrong way round. Easily resolved though took some head scratching to figure it out. Now I know why I spent so long drawing up that circuit diagram.
The indicator relay was suffering the same problem (reversed connections).
The oil pressure warning light had a loose bulb.
I didn't think that was at all bad for the first test of a completely custom built wiring loom. There are a few things I can't test as I haven't fitted them yet but still a nice result so far.
Here are a couple of pictures of the new dash in situ.
The fuel pumps and filter have been refitted in the boot ready for the tank to be plumbed in. I decided to make a better mounting for the tank than the odd bits of bracketry I had before so that's on hold until I can get hold of some aluminium box and angle to do some fabrication work.
This weekend I started by fitting the front lighting to the bonnet and quarter valences. The sidelight/indicator units fitted easily and so did the left hand headlamp but when I fitted the right hand headlamp it was obviously sitting at an angle and the cowl wouldn't fit over it either. After a lot of measuring I re-drilled the mountings so it would sit straight and also moved it over about 2mm. Such are the joys of working with a glass fibre bonnet.
After that the cowl still didn't fit and there followed a lot of fitting, dismantling, measuring, refitting, fabrication of spacers, dismantling again and so on. After a disproportionate amount of effort though it all eventually went together properly and everything lines up so it actually looks quite good.
I only stripped one thread in each of the cast alloy cowls too. They really are a poor design.
So that actually completed all the main work I had planned to do before the end of this month. Today however, with assistance from my dad we assembled the engine and gearbox and lifted it into the car.
I didn't really know whether it would fit as the new gearbox has never actually been in the car yet so I didn't know what problems we might encounter.
In the end the gearbox went in easily. There was a problem however and it certainly wasn't one I had anticipated...
Either my engine has shrunk whilst it's been sitting around the garage or there's something wrong with the mounting points onto the suspension turrets! One engine mount fits easily but the other is an inch short...
Here are some close-up photos of the problem.
After I took these pictures I noticed that the engine was also not sitting straight in the car. Unbolting the right hand mounting and bolting in the left hand one allowed the engine to sit vertical and nicely central in the engine bay and also central to the hole in the bulkhead but of course the one inch gap is now on the other side.
That leads me to believe that the problem might be somewhere around the right hand mounting but I can't see anything that's not where it should be. I've also done some measuring and as far as I can tell the suspension turrets are where they should be with the top wishbone mounting bolts equally spaced either side of the centre line.
We tried two different sets of engine mounts. One brand new and the other being the set that were on the engine previously. The back of the gearbox isn't fastened to anything and is free to move around so that can't be pulling anything out of line.
As far as I know there's only one type of suspension turret but I may be wrong there. Is it possible the turret from a different car has got in there during the rebuild? If you have any ideas, please feel free to leave comments below. Right now I'm out of ideas.
We both stared at this problem for quite a while and in the end we both gave up. I made a temporary bracket to hold the engine in position so that we could at least release it from the engine crane. I also started work on making a mounting bracket for the back of the new gearbox.
At least with the engine (roughly) in position I can get on with taking the measurements for the remainder of the wiring loom and I can also look at working out how things like the gearbox speed sender are going to fit. The gearbox seems quite close to the chassis at that point.
So several things sorted out but a new problem to deal with. Odd how these things come from the most unexpected directions sometimes.
Both fire extinguisher and battery are now fully fitted and I've tested all of the wiring that I can at this stage. The good news is that it all works! There were a few minor things wrong but they were soon sorted out. Specifically;
The headlight flash didn't work due to two terminals on the switch being the wrong way round. Easily resolved though took some head scratching to figure it out. Now I know why I spent so long drawing up that circuit diagram.
The indicator relay was suffering the same problem (reversed connections).
The oil pressure warning light had a loose bulb.
I didn't think that was at all bad for the first test of a completely custom built wiring loom. There are a few things I can't test as I haven't fitted them yet but still a nice result so far.
Here are a couple of pictures of the new dash in situ.
The fuel pumps and filter have been refitted in the boot ready for the tank to be plumbed in. I decided to make a better mounting for the tank than the odd bits of bracketry I had before so that's on hold until I can get hold of some aluminium box and angle to do some fabrication work.
This weekend I started by fitting the front lighting to the bonnet and quarter valences. The sidelight/indicator units fitted easily and so did the left hand headlamp but when I fitted the right hand headlamp it was obviously sitting at an angle and the cowl wouldn't fit over it either. After a lot of measuring I re-drilled the mountings so it would sit straight and also moved it over about 2mm. Such are the joys of working with a glass fibre bonnet.
After that the cowl still didn't fit and there followed a lot of fitting, dismantling, measuring, refitting, fabrication of spacers, dismantling again and so on. After a disproportionate amount of effort though it all eventually went together properly and everything lines up so it actually looks quite good.
I only stripped one thread in each of the cast alloy cowls too. They really are a poor design.
So that actually completed all the main work I had planned to do before the end of this month. Today however, with assistance from my dad we assembled the engine and gearbox and lifted it into the car.
I didn't really know whether it would fit as the new gearbox has never actually been in the car yet so I didn't know what problems we might encounter.
In the end the gearbox went in easily. There was a problem however and it certainly wasn't one I had anticipated...
Either my engine has shrunk whilst it's been sitting around the garage or there's something wrong with the mounting points onto the suspension turrets! One engine mount fits easily but the other is an inch short...
Here are some close-up photos of the problem.
After I took these pictures I noticed that the engine was also not sitting straight in the car. Unbolting the right hand mounting and bolting in the left hand one allowed the engine to sit vertical and nicely central in the engine bay and also central to the hole in the bulkhead but of course the one inch gap is now on the other side.
That leads me to believe that the problem might be somewhere around the right hand mounting but I can't see anything that's not where it should be. I've also done some measuring and as far as I can tell the suspension turrets are where they should be with the top wishbone mounting bolts equally spaced either side of the centre line.
We tried two different sets of engine mounts. One brand new and the other being the set that were on the engine previously. The back of the gearbox isn't fastened to anything and is free to move around so that can't be pulling anything out of line.
As far as I know there's only one type of suspension turret but I may be wrong there. Is it possible the turret from a different car has got in there during the rebuild? If you have any ideas, please feel free to leave comments below. Right now I'm out of ideas.
We both stared at this problem for quite a while and in the end we both gave up. I made a temporary bracket to hold the engine in position so that we could at least release it from the engine crane. I also started work on making a mounting bracket for the back of the new gearbox.
At least with the engine (roughly) in position I can get on with taking the measurements for the remainder of the wiring loom and I can also look at working out how things like the gearbox speed sender are going to fit. The gearbox seems quite close to the chassis at that point.
So several things sorted out but a new problem to deal with. Odd how these things come from the most unexpected directions sometimes.
Saturday 10 March 2012
The twit factor
In an attempt to enter the 21st century this blog now has a connection to Twitter!
I'll get one of those "follow" buttons on here eventually but in the meantime if you are suitable twitter-equipped you can look for @mikd43.
Apparently it's the future...
In more practical news, the race car now has the battery box and fire extinguisher trial fitted. I'm just waiting for a few bits and pieces I have on order before I can complete fitting these and lay in the plumbing for the extinguisher.
The fuse box is also fitted. On the electrical side the next step will be to install the dashboard and start testing the wiring. In the photograph below the fuse box is still only loosely fitted in case it has to come out again whilst I'm testing.
While all this work has been going on on the race car the road going Spitfire hasn't been forgotten. I am reliably informed that the bodywork on that car is finally complete and it will be moving to the paint shop next week.
That means I need to wind up work on the race car in order to clear the garage for when the other car comes back. The plan at the moment is to complete all the ongoing electrical work but if there is still time I'd like to offer up the engine and gear box assembly to see whether any major work is going to be required to get that to fit. If so I can plan that whilst I get on with reassembling the other car.
I'll get one of those "follow" buttons on here eventually but in the meantime if you are suitable twitter-equipped you can look for @mikd43.
Apparently it's the future...
In more practical news, the race car now has the battery box and fire extinguisher trial fitted. I'm just waiting for a few bits and pieces I have on order before I can complete fitting these and lay in the plumbing for the extinguisher.
The fuse box is also fitted. On the electrical side the next step will be to install the dashboard and start testing the wiring. In the photograph below the fuse box is still only loosely fitted in case it has to come out again whilst I'm testing.
While all this work has been going on on the race car the road going Spitfire hasn't been forgotten. I am reliably informed that the bodywork on that car is finally complete and it will be moving to the paint shop next week.
That means I need to wind up work on the race car in order to clear the garage for when the other car comes back. The plan at the moment is to complete all the ongoing electrical work but if there is still time I'd like to offer up the engine and gear box assembly to see whether any major work is going to be required to get that to fit. If so I can plan that whilst I get on with reassembling the other car.
Tuesday 6 March 2012
Riveting stuff!
I was in danger of grinding to a halt with the work on the race car last weekend but thanks to the loan of a compressor and an air powered riveter (thanks Paul!) things have moved forward a little.
Not the most exiting action-packed photographs here but you can see what I've been up to. Here's the new wiring harness installed running down the centre of the car.
You can just see part of the connection point under the dash where the various sections of harness plug together. At the rear the main battery feed cable splits off to where the battery will be located behind the driver's seat. The rest of the harness runs into the left rear wing to pass through to the boot.
The coiled black cable in the second photograph is for the electrically operated fire extinguisher which will mount in that space eventually.
Unfortunately I discovered that I'd forgotten to buy the necessary terminals to connect the rear lights so they are now on order and I'll be able to finish this section of the wiring once I have them.
I've also ordered the battery along with its housing box and the fire extinguisher system so the next job will be to fit those.
Not the most exiting action-packed photographs here but you can see what I've been up to. Here's the new wiring harness installed running down the centre of the car.
You can just see part of the connection point under the dash where the various sections of harness plug together. At the rear the main battery feed cable splits off to where the battery will be located behind the driver's seat. The rest of the harness runs into the left rear wing to pass through to the boot.
The coiled black cable in the second photograph is for the electrically operated fire extinguisher which will mount in that space eventually.
Unfortunately I discovered that I'd forgotten to buy the necessary terminals to connect the rear lights so they are now on order and I'll be able to finish this section of the wiring once I have them.
I've also ordered the battery along with its housing box and the fire extinguisher system so the next job will be to fit those.
Wednesday 22 February 2012
A new look
I thought it was about time the blog had a style update. I think it looks a bit better now. I can't promise that the quality of the content will improve much though!
Sunday 19 February 2012
How long is a piece of wire?
A lot of work has been completed on the wiring harness over the last few weeks. Here's a summary and a few photographs of the work in progress.
This is the starting point. 41 spools of differently coloured wire. It's quite a lot but not too hard to sort out once I stopped confusing "green" with "light green". Some of the colour combinations are a bit difficult to see in anything other than a good light though. "Green with Brown" for example. Let's hope I don't have too many problems that need sorting out under the dashboard once this lot is in the car!
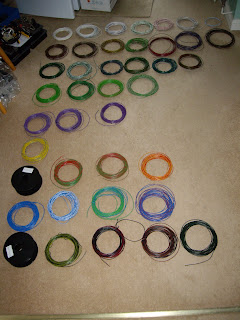
...and here's the work in progress. This is the main loom that fits behind the dashboard and includes the fusebox and all the instrument wiring. All the other sections will connect to this one so it is by far the most complex.The large sheets of paper are the drawing I mentioned in my last post showing where all the connections are supposed to go to and from.
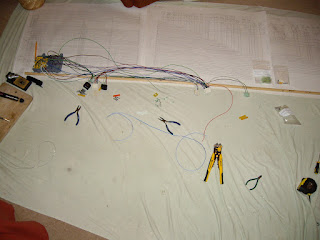
Can you tell what it is yet? This is probably about half finished.
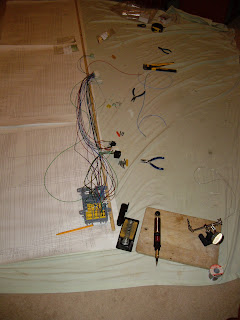
Almost done now. You can see the the whole thing in this picture. The fusebox is on the left, then the connectors for the other loom sections. More connectors in the middle for the dashboard switch panel and then the instruments further to the right.
The long sections sprawling out above the main loom are the pre-formed harnesses that came with the new instruments and provide power and lighting for them. I've modified these and spliced them into my wiring. At this stage they still need more modification before they will correctly reach all the instruments.
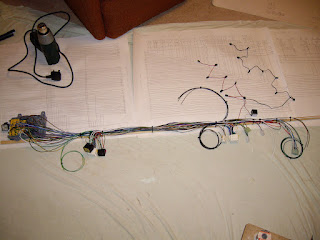
Just over a week of evenings and weekends since I started and this is the final result. You can see my master wiring diagram in this picture too.
After this the next two sections were much simpler and didn't take anything like as much effort. I've spent this weekend installing them in the car and so far it all looks good. Another weekend's work should see all the wiring complete except for the section that runs to the engine and the front of the car. I can't build that section until the engine is back in since there are no reference points from which to take measurements at the moment.
This is the starting point. 41 spools of differently coloured wire. It's quite a lot but not too hard to sort out once I stopped confusing "green" with "light green". Some of the colour combinations are a bit difficult to see in anything other than a good light though. "Green with Brown" for example. Let's hope I don't have too many problems that need sorting out under the dashboard once this lot is in the car!
...and here's the work in progress. This is the main loom that fits behind the dashboard and includes the fusebox and all the instrument wiring. All the other sections will connect to this one so it is by far the most complex.The large sheets of paper are the drawing I mentioned in my last post showing where all the connections are supposed to go to and from.
Can you tell what it is yet? This is probably about half finished.
Almost done now. You can see the the whole thing in this picture. The fusebox is on the left, then the connectors for the other loom sections. More connectors in the middle for the dashboard switch panel and then the instruments further to the right.
The long sections sprawling out above the main loom are the pre-formed harnesses that came with the new instruments and provide power and lighting for them. I've modified these and spliced them into my wiring. At this stage they still need more modification before they will correctly reach all the instruments.
Just over a week of evenings and weekends since I started and this is the final result. You can see my master wiring diagram in this picture too.
Monday 30 January 2012
Dash hackery and other garage fumblings
Having got all the rear lights fitted towards the end of last year (which sounds like it's a long time off now!) I moved on to getting my new dashboard to fit.
A surprising amount of metal had to be removed to allow for the new instrument panel to fit, mostly due to the new instruments having larger fixings on the back than the original ones. They are exactly the same size at the front. I spent several evenings cutting the metal panel behind the dash and offering up the instrument panel.
Once that was done I went on to drill out some spot welds and remove a few unnecessary brackets. This car doesn't have heater, radio or glove boxes so all the associated metalwork to support them has now gone.
I have trial fitted the complete dash and it all fits nicely although I was obviously a little too enthusiastic in removing metal from the top edge of the hole behind the instruments which shows above the front panel as do the holes where I removed the heater bracket. That's no problem though as it should be easily possible to tidy that later.
The dash panels have now been removed again in preparation for starting to fit the wiring loom.
I've been working on a complete custom wiring diagram for the car and I now think I have the final version of that. I spent most of last weekend translating the logical diagram into a map of exactly where each individual wire should route in the car, where it comes from and goes to and what connector it should have on the end. That was a lot of work but it will make the job of actually constructing the loom vastly easier.
The final hand drawing is currently occupying three sheets of A1 paper. The next step is to redraw it all on the computer and hopefully scale it down to more manageable A4 sheets.
Spurred on by my success in cutting away metal to get the dash to fit I went on to start fitting the new fuse box. I have a modern fuse and relay box to fit and the plan is to put it in the original battery tray. The battery itself is to be located in the back of the car.
What was needed was a large hole for the wiring to pass through from the fuse box to the inside of the car. I started the job with a drill mounted hole cutter but that ground all the teeth off the cutter and made very little impression on the panel... it was a cheap cutter and now I know why!
Since my Dremel rotary multi-tool had been very successful on the dash panel I tried that next and although it managed about eighty percent of the way round the hole it had obviously had enough after all the work on the dash and it shorted out and expired.
A new hacksaw I'd bought in case it was useful for all this cutting fell apart within seconds so I was left to complete the hole with an old "side cutting drill bit" in my power drill. It's not the best tool in my box but it got the job done.
The net result of all this is a large-but-not-quite-round hole in the bottom of the battery tray. After that, drilling the four bolt holes in the right places to mount the fuse box seemed quite easy! Fortunately the large hole won't be visible once the fuse box is fitted.
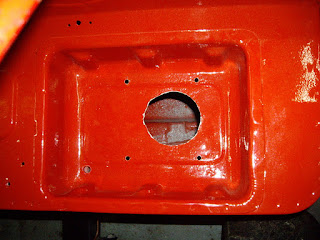
In between all this lot I've been making some progress on my gearbox as well. I need to try and remember to write a whole post about that part of the project but I actually got as far as trial fitting all the parts and bolting the whole thing together last Friday and remarkably it actually seems to fit. I've now ordered a new clutch and fittings. Once I have those I can reassemble it for the final time and that will be a huge step forward.
Away from the race car I am reliably informed that my road car now has a rolling chassis and the bodywork is almost complete too. I checked on the engine rebuild this week and that only needs a few minor parts so should be finished within a few days. Once the road car rolling shell is painted it will be coming back here and the race car project will have to go on hold until the road car is finished. There's a lot I need to get done before then!
A surprising amount of metal had to be removed to allow for the new instrument panel to fit, mostly due to the new instruments having larger fixings on the back than the original ones. They are exactly the same size at the front. I spent several evenings cutting the metal panel behind the dash and offering up the instrument panel.
Once that was done I went on to drill out some spot welds and remove a few unnecessary brackets. This car doesn't have heater, radio or glove boxes so all the associated metalwork to support them has now gone.
The dash panels have now been removed again in preparation for starting to fit the wiring loom.
I've been working on a complete custom wiring diagram for the car and I now think I have the final version of that. I spent most of last weekend translating the logical diagram into a map of exactly where each individual wire should route in the car, where it comes from and goes to and what connector it should have on the end. That was a lot of work but it will make the job of actually constructing the loom vastly easier.
The final hand drawing is currently occupying three sheets of A1 paper. The next step is to redraw it all on the computer and hopefully scale it down to more manageable A4 sheets.
Spurred on by my success in cutting away metal to get the dash to fit I went on to start fitting the new fuse box. I have a modern fuse and relay box to fit and the plan is to put it in the original battery tray. The battery itself is to be located in the back of the car.
What was needed was a large hole for the wiring to pass through from the fuse box to the inside of the car. I started the job with a drill mounted hole cutter but that ground all the teeth off the cutter and made very little impression on the panel... it was a cheap cutter and now I know why!
Since my Dremel rotary multi-tool had been very successful on the dash panel I tried that next and although it managed about eighty percent of the way round the hole it had obviously had enough after all the work on the dash and it shorted out and expired.
A new hacksaw I'd bought in case it was useful for all this cutting fell apart within seconds so I was left to complete the hole with an old "side cutting drill bit" in my power drill. It's not the best tool in my box but it got the job done.
The net result of all this is a large-but-not-quite-round hole in the bottom of the battery tray. After that, drilling the four bolt holes in the right places to mount the fuse box seemed quite easy! Fortunately the large hole won't be visible once the fuse box is fitted.
In between all this lot I've been making some progress on my gearbox as well. I need to try and remember to write a whole post about that part of the project but I actually got as far as trial fitting all the parts and bolting the whole thing together last Friday and remarkably it actually seems to fit. I've now ordered a new clutch and fittings. Once I have those I can reassemble it for the final time and that will be a huge step forward.
Away from the race car I am reliably informed that my road car now has a rolling chassis and the bodywork is almost complete too. I checked on the engine rebuild this week and that only needs a few minor parts so should be finished within a few days. Once the road car rolling shell is painted it will be coming back here and the race car project will have to go on hold until the road car is finished. There's a lot I need to get done before then!
Saturday 7 January 2012
The slightly delayed Christmas update
A very brief update today. I meant to post this before Christmas but never got around to it. I spent some time painting bits and pieces and fitting them. Its amazing how much time can be taken up with fiddly little tasks but the car now has a windscreen wiper rack and a complete set of rear lights.
Much more to do soon!
Subscribe to:
Posts (Atom)